powder coating.
For individual parts and batches of all sizes
powder coating
Surface finishing refers to all processes used to treat a workpiece or product in order to improve performance-related factors such as enhancing its weather resistance or aesthetics. The XBond Group has been harnessing our specialist expertise, high quality standards, dedication, flexibility, service and fair prices for the benefit of our happy customers since 1981.
If you’re looking for a particularly hard, scratch-resistant and beautiful finish, powder coating is the perfect choice. Powder coating offers a wide range of benefits over other coating methods. It’s a highly eco-friendly industrial process as it doesn’t use solvents, which are known to be harmful to the environment.
Steel components that are primed with Bonderite can also be given a final powder coating at a later point in time.
Alongside our XBond manufacturing expertise, we are passionate about products from all areas of the metal processing industry, including those from commercial vehicle and passenger vehicle suppliers, makers of tubular furniture, fire protection, animal stalls, machinery, furnishings, shop fittings and trade show booths, in large and small quantities.
Pre-treatment
Process
Powder coatings
Part size
Advice on aftercare
XBond manufacturing expertise
Where powder coating is used
At its core, powder coating is a universal coating process. In combination with our expertise in the field of crevice finishing in the steel sector, we truly come into our own in the following specialist applications::
high-tensile steels – complex geometries – upstream masking area
1 Pre-treatment
A range of pre-treatment processes (conversion treatment), blasting and de-greasing ensure that the scratchproof powder coating bonds with the surface smoothly and permanently.
2 Process
This pre-treatment sees the substrates immersed in our pre-treatment tanks to remove grease and dirt, then coated with a conversion layer that protects the material from corrosion and assists with adhesion. The parts are then rinsed and dried to ensure that the surface pre-treatment is effective.
Special feature: Bonderite M-PP 930 and powder are applied and cured together to form an inseparable layer. Traditional metal pre-treatment and the subsequent coating are combined into one process as standard.
The powder is applied with an automatic system or manually if required. The powder coating is then heated to 180 °C in a curing oven. This creates an incredibly durable, impact-resistant surface
3 Powder coatings
Powder coatings are dry, powdered materials that are applied to workpieces using an electrostatic or similar process, then heated to adhere them in place. This triggers a chemical reaction which gives the coating its excellent characteristics. Powder coating can deliver almost any conceivable finish, such as gloss, matt, textured or metallic effects.
Antibacterial
Powder coating with an antibacterial effect prevents the spread of dangerous microorganisms and mould and bacteria from growing. Its main areas of application are in the pharmaceutical industry, hospitals, air conditioning and ventilation systems and household appliances.
Anti-graffiti
Powder coating as an anti-graffiti treatment boasts outstanding chemical resistance. It creates surfaces that are almost impervious to all kinds of graffiti. Spray paints can be removed without leaving any residue.
Photoluminescent
Fluorescent powder coating reacts to longwave UV radiation, also known as blacklight. UV-sensitive pigments within the coating absorb the blacklight and produce visible light.
Highly heat-resistant
Heat-resistant powder coating provides for good adhesion and long-term resistance to high temperatures.
4 Part size
The maximum part size is 8,000 mm in length, 800 mm in width and 1,600 mm in height, with a maximum part weight of 350 kg.
5 Advice on aftercare
Gentle care and maintenance for powder-coated surfaces:
- Just use water. If a detergent is used, this must be as neutral as possible (pH value: 5-8)
Do not use acidic or strong alkaline detergents - Use detergents with a known composition
- The surface temperature should not exceed 25°C during cleaning
- Avoid cleaning in direct sunlight
- Use a soft, clean sponge
- Immediately rinse with clean water after cleaning
- Do not use a steam cleaner or pressure washer!
6 XBond manufacturing expertise
Our broad manufacturing expertise enables us to offer you a wide range of options for component processing. The secret to versatile manufacturing is a combination of a strong team, speed, minimal complexity, knowing what is possible, a healthy dose of common sense and availability of resources.
Steps to achieving optimal pre-treatment
(free from solvents and heavy metals)
GSB and Qualicoat certification
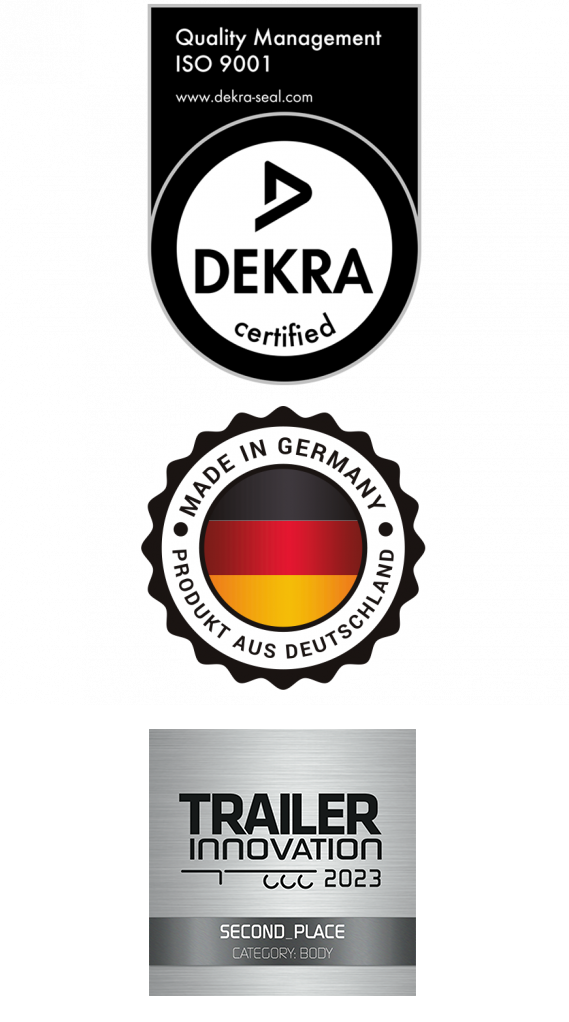
Leistungen
Kontakt
XBond GmbH & Co.KG
Im Garbrock 29
48683 Ahaus-Ottenstein,
Deutschland
Telefon: 02561 / 9831-0
Telefax: 02561 / 9831-31
Schreiben Sie uns